Instinct to Digital Impact: Integrating Mindesk into our Design Workflow
Lorena Knezevic, Perkins&Will Miami Studio
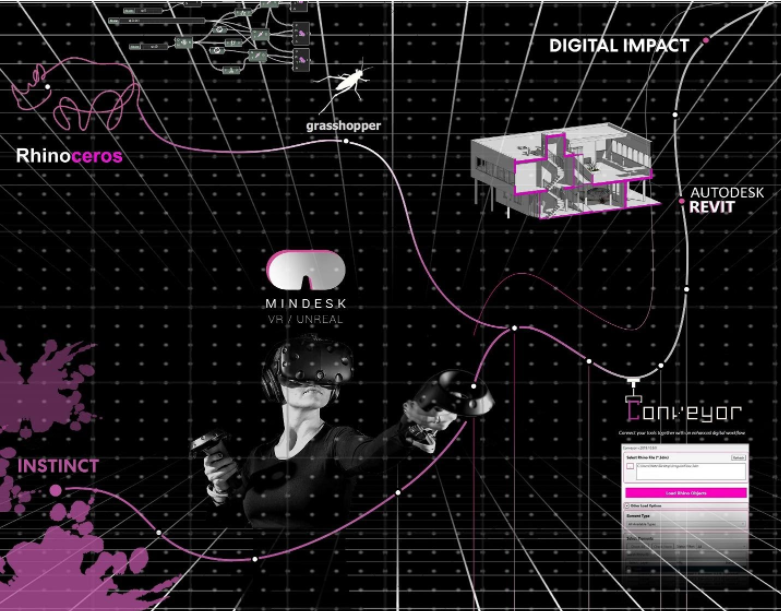
Perkins&Will has always pushed the limits of technology—and Virtual Reality is no exception. As designers, we’re empowered to immerse ourselves in our projects, using VR as both a visualization tool and as a means to model in real-time. Our firm actively invests in investigations through programs such as Innovation Incubator, which supports design-focused research by providing micro-grants of money and time. Open to everyone at the firm, the program provides grant recipients money and time to explore topics of their choosing. As a grant recipient, I chose to study how a designer’s instinct can now be captured, quantified, and have digital impact in real time. My project, Instinct to Digital Impact, was a recommended workflow that integrates Mindesk into our existing process.
Innovation Incubator: Instinct to Digital Impact
Thus far, intuition has been nearly impossible to be describe metrically. Designers have relied on tools to translate their three-dimensional mental constructs into a two-dimensional drawing space through a pen or a computer mouse. Mindesk offers designers a kinesthetic, “tangible” relationship to the design in real-time, replacing a computer mouse with hand controllers that guide movements in a virtual space.
Additionally, the designer has an opportunity to walk in and around their model while making design changes. In effect, the designer’s instinct can become the thread that connects each software, allowing a single design decision made in a virtual reality environment to instantly impact the the design process.
This study implements the programs Rhino (McNeel), Mindesk, Conveyor (by Proving Ground) and Revit (Autodesk), creating links between the programs to operate efficiently in an iterative design process. Here, virtual reality is used both as a visualization and as a digital modeling tool through many stages of design with the proposed workflow.
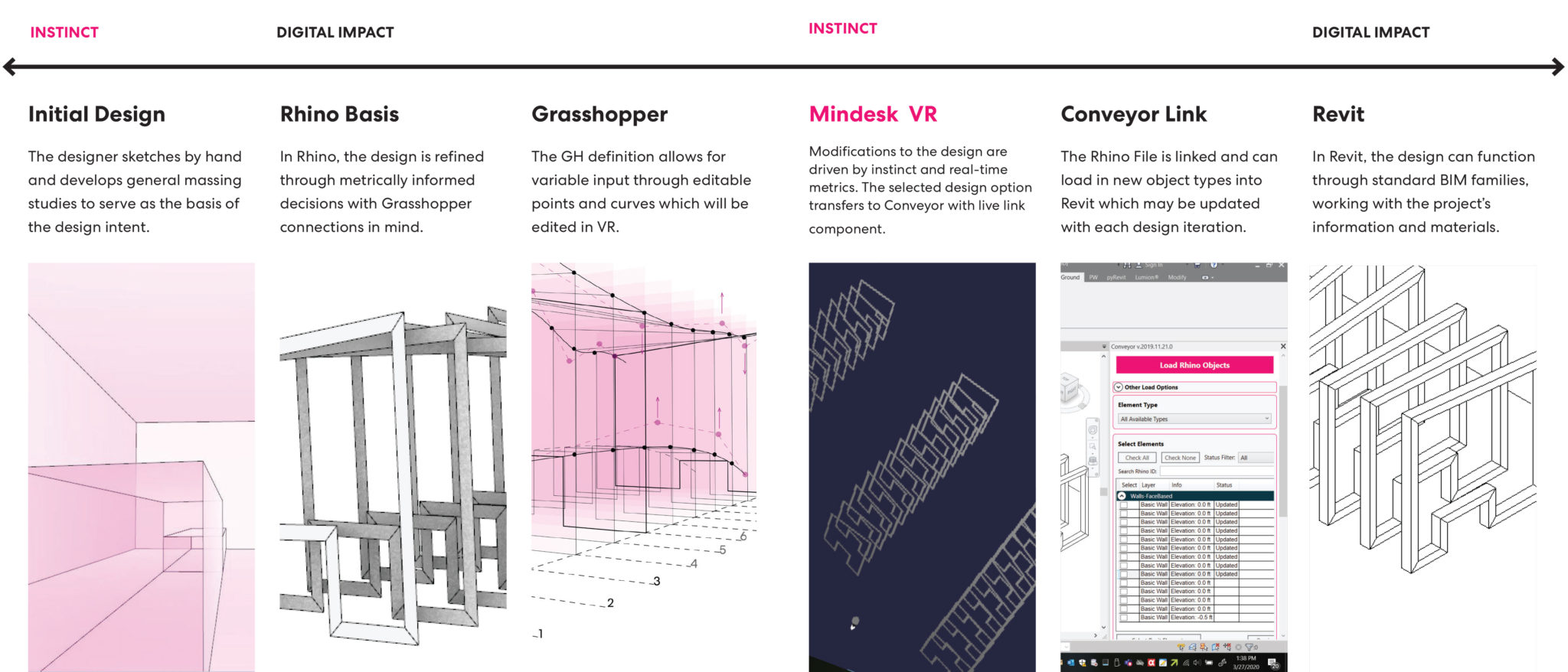
The Workflow
1. The initial design is conceived of through hand sketches and explored as a schematic massing in Rhino.
2. Grasshopper can be used to create a definition, which generates variations of a design based on specific parameters such as the height or location of control points along a curve, or the shape of a geometry.
3. Mindesk VR is a plug-in that can be launched directly from Rhino, offering an additional viewport of the design. Here, the designer can begin modifying the shape instinctively while receiving metrics within the virtual reality environment. These metric changes directly affect the real digital content. Additionally, if the changes are being made to a control point that is connected to a Grasshopper definition, the designer can see the effect of their design decisions as a Grasshopper result developed in real time.
4. The same Grasshopper definition, which was integrated as part of the initial design and was manipulated by the instinctive design decisions in virtual reality, can also create a “live” link to Conveyor. The definition automatically prepares a Rhino 3DM file type to import into Revit, regardless of the amount of design changes. Though the import process is not live, the simple few-click steps in this testing stage make it an efficient workflow.
5. Within the Revit environment, the designer can use Conveyor to import the previously designed geometry. These geometries can be updated at every step of the design process. If a geometry is imported as a wall-based family, the face will update as the Rhino geometry changes.
6. Design modifications in Revit can continue just as any other design process. With a “live” link established from the VR environment, the intuitive design decisions may influence the same geometries used for construction documentation. Instinct can have digital impact.
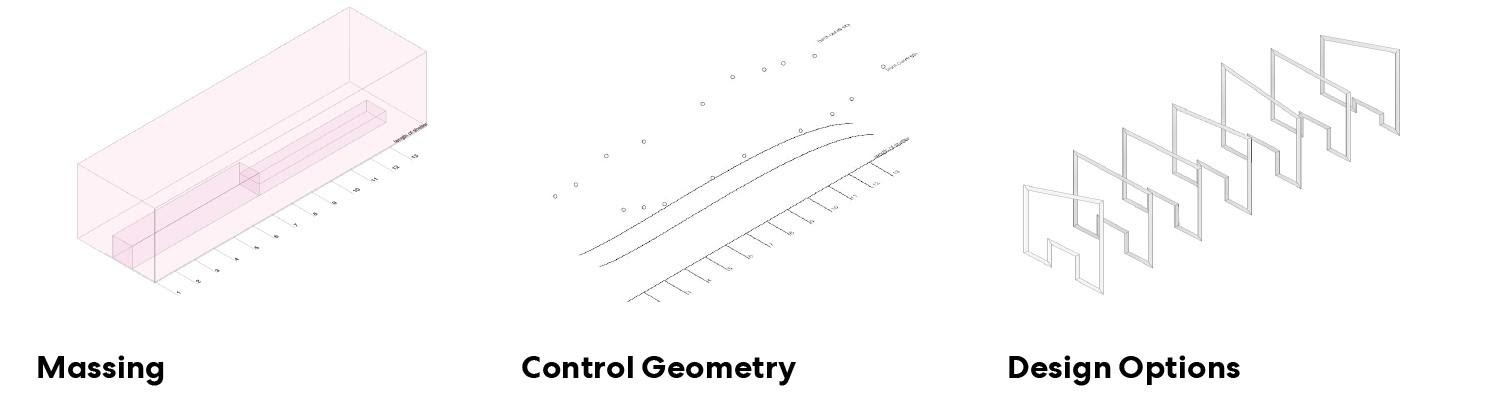
Rhino + MindeskVR
To fully understand the possibilities and challenges of this proposed workflow, I needed to test it on a hypothetical project. I proposed options for a multimodal transportation shelter, beginning with a massing study in Rhino, which I further defined with a series of geometries including points and curves. Next, I created a Grasshopper definition that relied on specific control points that existed as real objects in the Rhino workspace. This technique is especially helpful when creating design options in MindeskVR. Within VR, I could select the pre-determined control points with hand-held controllers and instinctively modify their locations. If the Grasshopper definition is strategically linked to these specific points, a designer would be able to see real-time parametric modifications to their designs at a 1:1 scale in MindeskVR.
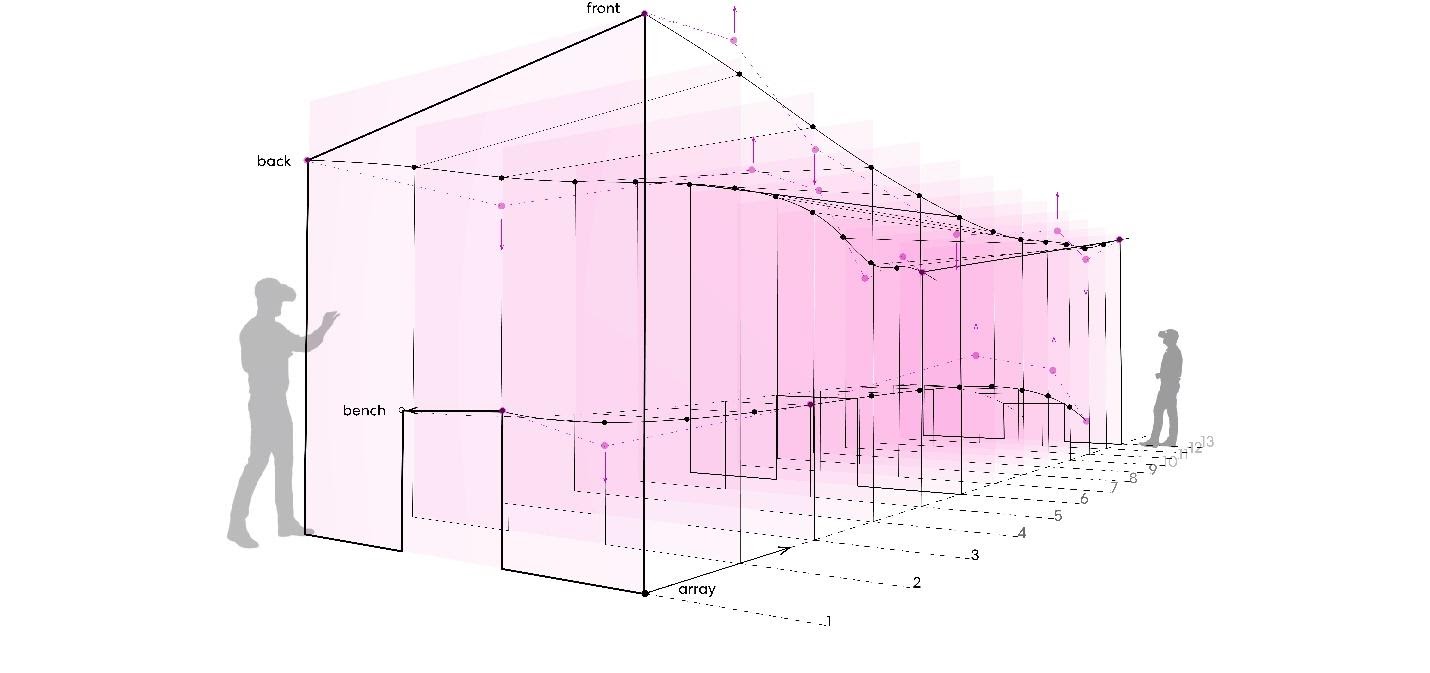
Using Grasshopper to define the geometry provides greater flexibility in virtual reality modifications as well as cleaner geometry exports into Revit. However, it is important to note that even though Grasshopper was incorporated into this proposed workflow, the effect of VR modifications can be achieved with Rhino modeling in MindeskVR. The critical difference would be the way the geometry is exported to Conveyor.
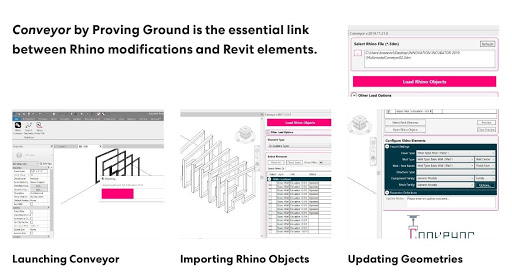
MindeskVR + Conveyor
Conveyor by Proving Ground is a plugin designed for Autodesk Revit that allows for Rhino geometries to become imported into Revit as objects that are editable with Revit parameters. Within Rhino, there are two ways to prepare the files to identify which geometries should be converted to specific family types: Through a Conveyor + Rhino Plugin and layer organization or through a Conveyor + Grasshopper plugin attached to the output geometry in a definition.
MindeskVR has an excellent interface for Grasshopper that allows us to see a panel of the definition while remaining in the virtual world. I was able to link all the critical connections between software through a single Grasshopper definition – including the design definition and plugins to Conveyor for Revit. If the design has been updated in either Rhino or through MindeskVR, Conveyor in Revit will recognize that there are new geometries to update.
As I learned from testing, once this link between Rhino, MindeskVRGrasshopper, Conveyor, and Revit has been established initially, the design process can become iterative and limitless. From within MindeskVR, a designer can make modifications in virtual reality and with the toggle of one button update the source file, create real-time geometry changes in Revit.
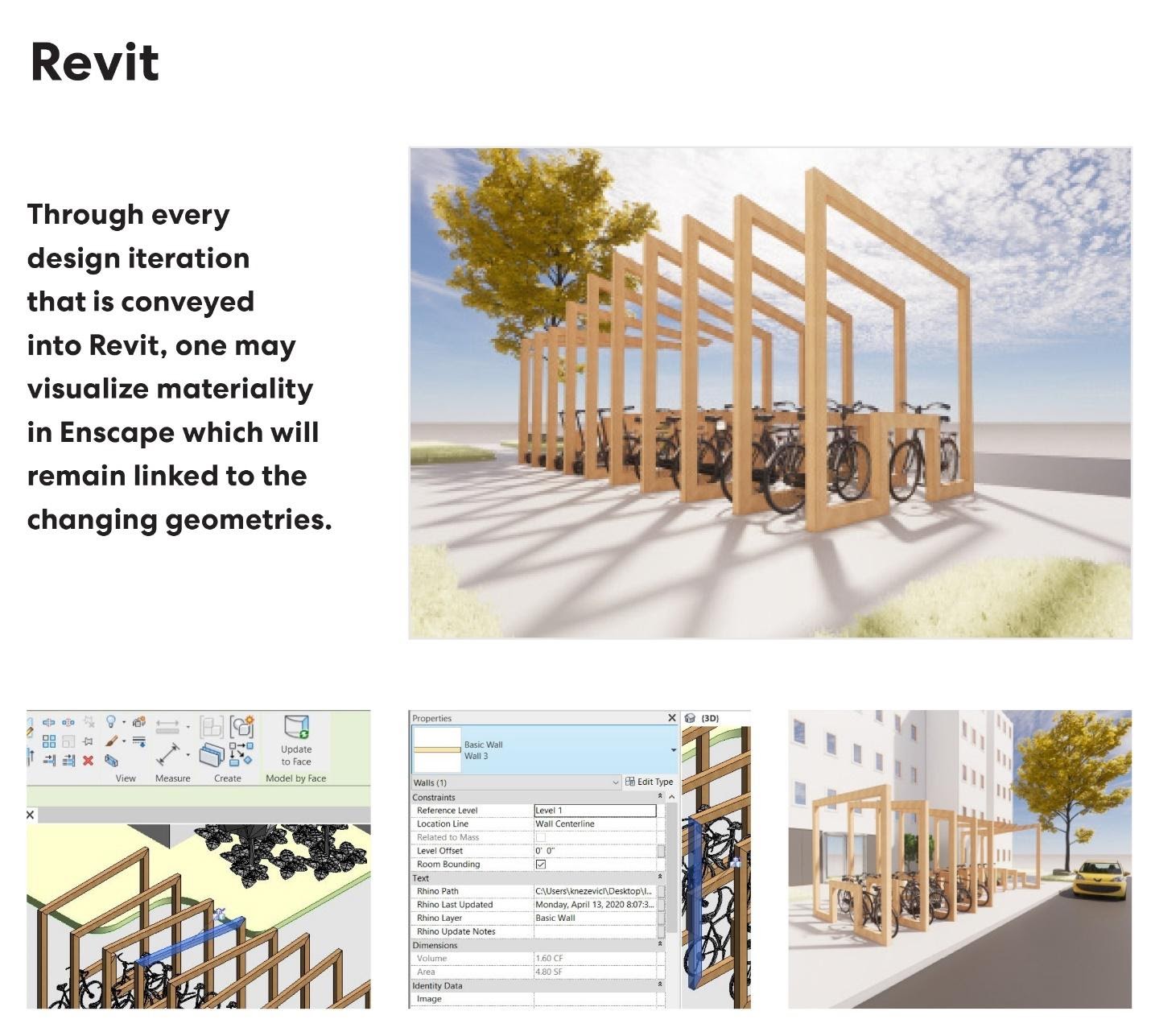
Conveyor + Revit
Many of the geometries imported into Revit through Conveyor will allow the designer to make modifications to the Revit components while retaining the live link to the origin Rhino geometry. Here in this wall-by-face basic wall family, the Rhino geometry is not visible but acts as a Revit Mass would, defining the limits of the wall surface. When the Rhino geometry is updated, we will be able to “Update to Face” to accept the changes to the wall family, However, if the origin geometry has moved entirely or been deleted, these changes will not take effect.
If there are many design options developed in MindeskVR, a designer can also import them as design options in Revit with the same geometry-linking techniques. At Perkins&Will, all these tools are readily available to us. With the introduction of MindeskVR, we are able to adjust and enhance our designs in an entirely new way.
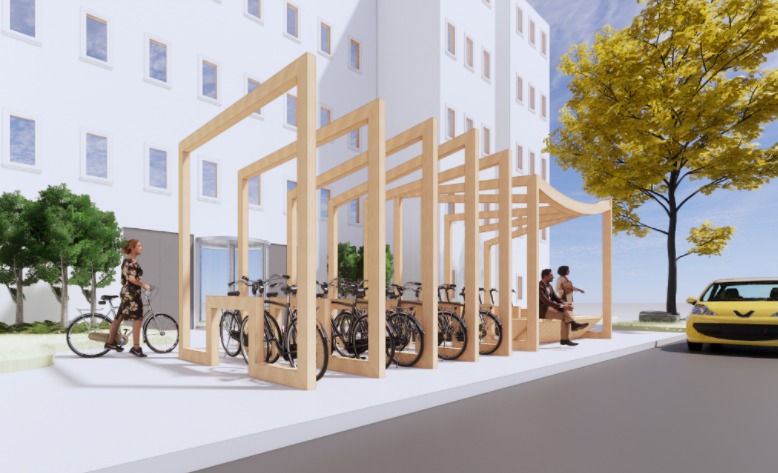
Reflections
Throughout the process of designing a multimodal transportation center, I evaluated the benefits of using virtual reality at a 1:1 scale to test human comfort. The ability to maneuver around posts while parking a bicycle or assess the views underneath the canopy were influenced by instinctive design decisions. I was able to move specific attractor points which were within arm’s reach to adjust heights of control points, impacting the perspective view lines. This process revealed that the transportation center needed more undulations in the controlling curve for enhanced visual interest. Initially when I was creating a baseline geometry on my desktop, I had predicted that only one twisting of the structure would have been enough to provide intrigue. However, when seen at an eye-level perspective, the changes in the geometry were so subtle that they were hardly noticeable. In the MindeskVR environment, I was able to edit and immediately see the resulting geometries as a design option.
Through my proposed workflow, a designer can create an infinite number of design options, making decisions based on real-time experiences at a 1:1 scale. These changes might involve widening of passageway openings or changing undulations of the overall geometry. At any point, the designer’s instinctive changes are captured in a three-dimensional and impactful manner.
Read more at innovation.perkinswill.com.